 |
Figure 1 |
The kraft process is the dominant pulping process in the United States, accounting for approximately 85 percent of all domestic pulp production. The soda pulping process is similar to the kraft process, except that soda pulping is a non-sulfur process. One reason why the kraft process dominates the paper industry is because of the ability of the kraft chemical recovery process to recover approximately 95 percent of the pulping chemicals and at the same time produce energy in the form of steam. Other reasons for the dominance of the kraft process include its ability to handle a wide variety of wood species and the superior strength of its pulp.
The production of kraft and soda paper products from wood can be divided into three process areas:
- Pulping of wood chips
- Chemical recovery
- Product forming (includes bleaching)
The relationship of the chemical recovery cycle to the pulping and product forming processes is
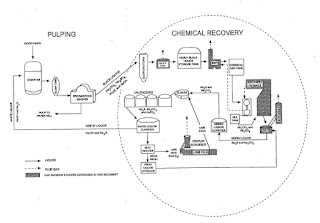 |
Figure 2 |
shown in Figure 1. Process flow diagrams of the chemical recovery area at kraft and soda pulp mills are shown in Figures 1 and 2, respectively.
The purpose of the chemical recovery cycle is to recover cooking liquor chemicals from spent
cooking liquor. The process involves concentrating black liquor, combusting organic compounds, reducing inorganic compounds, and reconstituting cooking liquor.
Cooking liquor, which is referred to as "white liquor, is an aqueous solution of sodium hydroxide (Na01) and sodium sulfide (Na2S) that is used in the pulping area of the mill. In the pulping process, white liquor is introduced with wood chips into digesters, where the wood chips are "cooked" under pressure. The contents of the digester are then discharged to a blow tank, where the softened chips are disintegrated into fibers or "pulp. The pulp and spent cooking liquor are subsequently separated in a series of brown stock washers: Spent cooking liquor, referred to as "weak black liquor, from the brown stock washers is routed to the chemical recovery area. Weak black liquor is a dilute solution (approximately 12 to 15 percent solids) of wood lignins, organic materials, oxidized inorganic compounds (sodium sulfate (Na2SO4), sodium carbonate (Na2003)), and white liquor (Na2S and Na0H).
In the chemical recovery cycle, weak black liquor is first directed through a series of multiple-effect evaporators (MEE's) to increase the solids content to about 50 percent. The "strong. (or "heavy") black liquor from the MEE's is then either oxidized in the BLO system if it is further concentrated in a DCE or routed directly to a concentrator (NDCE). Oxidation of the black liquor prior to evaporation in a DCE reduces emissions of TRS compounds, which are stripped from the black liquor in the DCE when it contacts hot flue gases from the recovery furnace. The solids content of the black liquor following the final evaporator/concentrator typically averages 65 to 68 percent.
Concentrated black liquor is sprayed into the recovery furnace, where organic compounds are combusted, and the Na2SO4 is reduced to Na2S. The black liquor burned in the recovery furnace has a high energy content (13,500 to 15,400 kilojoules per kilogram (kJ/kg) of dry solids (5,800 to 6,600 British thermal units per pound {Btu/lb} of dry solids)), which is recovered as steam for process requirements, such as cooking wood chips, heating and evaporating black liquor, preheating combustion air, and drying the pulp or paper products. Particulate matter (PM) (primarily Na2SO4) exiting the furnace with the hot flue gases is collected in an electrostatic precipitator (ESP) and added to the black liquor to be fired in the recovery furnace. Additional makeup Na2SO4, or "saltcake," may also be added to the black liquor prior to firing.
Molten inorganic salts, referred to as "smelt," collect in a char bed at the bottom of the furnace. Smelt is drawn off and dissolved in weak wash water in the SDT to form a solution of carbonate salts called "green liquor," which is primarily Na2S and Na2CO3. Green liquor also contains insoluble unburned carbon and inorganic Impurities, called dregs, which are removed in a series of clarification tanks.
Decanted green liquor is transferred to the causticizing area, where the Na2CO3 is converted to NaOH by the addition of lime (calcium oxide [Ca0]). The green liquor is first transferred to a slaker tank, where Ca0 from the lime kiln reacts with water to form calcium hydroxide (Ca(OH)2). From the slake, liquor flows through a series of agitated tanks, referred to as causticizers, that allow the causticizing reaction to go to completion (i.e., Ca(OH)2 reacts with Na2CO3 to form NaOH and CaCO3).
The causticizing product is then routed to the white liquor clarifier, which removes CaCO3 precipitate, referred to as "lime mud." The lime mud, along with dregs from the green liquor clarifier, is washed in the mud washer to remove the last traces of sodium. The mud from the mud washer is then dried and calcined in a lime kiln to produce "reburned" lime, which is reintroduced to the slaker. The mud washer filtrate, known as weak wash, is used in the SDT to dissolve recovery furnace smelt. The white liquor (NaOH and Na2S) from the clarifier is recycled to the digesters in the pulping area of the mill.
At about 7 percent of kraft mills, neutral sulfite semi-chemical (NSSC) pulping is also practiced. The NSSC process involves pulping wood chips in a solution of sodium sulfite and sodium bicarbonate, followed by mechanical de-fibrating. The NSSC and kraft processes often overlap in the chemical recovery loop, when the spent NSSC liquor, referred to as "pink liquor," is mixed with kraft black liquor and burned in the recovery furnace. In such cases, the NSSC chemicals replace most or all of the makeup chemicals. For Federal regulatory purposes, if the weight percentage of pink liquor solids exceeds 7 percent of the total mixture of solids fired and the sulfidity of the resultant green liquor exceeds 28 percent, the recovery furnace is classified as a "cross-recovery furnace.'" Because the pink liquor adds additional sulfur to the black liquor, TRS emissions from cross recovery furnaces tend to be higher than from straight kraft black liquor recovery furnaces.
With over 70 years experience,
Thompson Equipment Company, Inc. (TECO) provides specialized instrumentation, magnetic flow meters, and re-manufactured process instruments used in the pulp and paper industry. For information on process control instruments, valves, or service or calibration, visit
http://www.teco-inc.com or call 800-528-8997.