 |
Animation of differential flow |
Common to most
flowmeters are rated levels of performance; some of the more universal
performance metrics include accuracy, precision/repeatability, turndown ratio, resolution, ease of installation, straight pipe run requirements, on-going operations and maintenance, and costs.
Accuracy
Accuracy is the difference between a measured value and the actual value. No flowmeter is 100% accurate and most manufacturers provide a range of accuracies in their product line - tighter accuracy requirements are typically more expensive and may also be more restrictive to specific applications.
Precision/Repeatability
The precision or repeatability of a measurement entails the ability to reproduce the same value (e.g., flow rate) with multiple measurements of the same parameter, under the same conditions.
Turndown Ratio
The turndown ratio refers to the flow rates over which a meter will maintain a certain accuracy and repeatability. For example, a steam flow meter that can measure accurately from 1,000 pounds per hour (pph) to 25,000 pph has a turndown ratio of 25:1. The larger the turndown ratio, the greater the range over which the meter can measure the parameter within the accuracy stated.
Resolution
The resolution is the smallest increment of flow that can be incrementally registered by the meter. For example, a water meter designed for a small diameter pipe may be able to provide a resolution of 100 pulses per gallon (or more) as a signal output, but a meter designed for a larger pipe or higher maximum flow may only be able to provide 1 pulse per 100 gallons. Further, a very large flow meter may only be able to provide 1 pulse per 1000 gallons. The metering system may have limitations with regard to peak signal frequency or minimum time between pulses to properly register the data signal.
Ease of Installation
Select make-and-model decisions considering size and weight constraints, specific electrical and communications needs, and the overall environment the flowmeter will operate in.
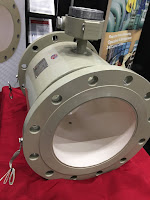 |
Magnetic flowmeter (TECO) |
Straight-pipe Run Requirements
Applicable to some types of fluid (gas, liquid and steam) flowmeters, straight-pipe run requirements relate to the length of unobstructed straight pipe required leading up to and immediately following the flow meter’s location. Obstructions in the fluid flow (such as elbows, tees, filters, valves, and sensor fittings) cause changes in the flow pattern (flow regime and velocity profile). Straight-pipe runs allow the flow pattern to normalize/stabilize making measurements by velocity-type and differential-pressure-type flow meters less prone to measurement error. Straight-pipe run requirements are usually expressed in terms of the number of pipe diameters.
The straight pipe requirement is in addition to the length of the flowmeter itself. The straight-pipe run requirements can be reduced with the addition of flow straightening or flow conditioning devices installed upstream.
Ongoing Operations and Maintenance
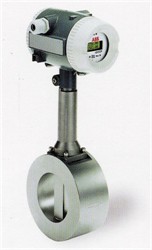 |
Vortex flowmeter (ABB) |
The lowest cost flow metering technology may not be the best choice if it has high associated maintenance costs (e.g., frequent service, calibration and recalibration, sensor replacement). As with most capital purchases, a life-cycle cost approach (including all capital and recurring costs) is recommended for decision making.
Installation Versus Capital Cost
In some situations, the cost to install a flowmeter can be greater than the capital cost; this can be true where system shutdowns are necessary for flowmeter installations, or where significant redesign efforts are needed to accommodate a flowmeter’s physical size, weight, or required connection. In these cases, decision makers should consider alternative technologies that may have a higher capital cost but a much lower installed cost. A good example of this is the use of non-intrusive flow metering technologies (e.g., ultrasonic flowmeters) that typically have a high capital cost but often a significantly reduced installed cost. It is recommended that meters be installed with isolation valves or switches making it easier to remove, replace, or service the meter in the future.
Reprinted and abstracted from US Department of Energy paper titled "Metering Best Practices: A Guide to Achieving Utility Resource Efficiency, "