Providing educational information on flowmeters, industrial control, process instrumentation, valves, and valve automation. Posts include interesting and unique industrial control applications, new product information, and ways of improving efficiency and saving money through proper maintenance, repair, service, and re-manufacturing.
Courtesy of Thompson Equipment Company | TECO-INC.COM | (504) 833-6381
Magnetic Flow Meters with Specialized Construction Still the Best Bet for Dredging Applications
Electromagnetic flow meters commonly measure slurry mixture flow on cutter suction dredgers and trailing suction hopper dredgers. These type of flow meters use exposed electrodes and non-conductive flow tubes. Ordinary magnetic flow meter flow tubes are not designed to withstand the abrasive conditions prevalent in dredging. Standard magnetic flow meter electrodes are prone to wear, breakage, and polarization requiring frequent re-adjustment. Standard electrode seals may also deteriorate and cause leaks and false readings.
As an alternative, non-invasive (non-wetted) flow meters, such as clamp-on or Doppler ultrasonic flow meters, have long been proposed because of their ease of installation and maintenance savings. However, testing of clamp-on or Doppler ultrasonic flow meters has never panned out in dredging applications. While there has been limited success on smaller sized diameters, there are few, if any, large diameter dredging pipe application success stories.
Dredging engineers always seek the simplest and most accurate method of measuring slurry flow. Considering this, there is convincing evidence that the use of customized electromagnetic flow meters, specifically designed to stand up to the rigors of dredging, look to be the best overall option.
Dredging-specific flow meters provide wear solutions that can extend the life of equipment and keep systems at maximum operational levels. Some users report life span up to 10 years.
The dredging modifications include custom engineered ceramic brick or polyurethane liners, 3/4" stainless steel inlet and outlet protectors, independently sealed electrode wells, and field accessible Hastelloy B electrodes.
Thompson Equipment (TECO), a manufacturer of severe service magnetic flow meters located in New Orleans, will "remanufacture" any make or model of electromagnetic flow meter for dredging service. They have decades of experience servicing and remanufacturing instrumentation, and are leaders in building severe service flow meters.
Electromagnetic flow meters have always been appealing for dredging applications in terms of accuracy, resolution, and response time. Their performance problems, caused by the direct and continuous flow of abrasive slurries, are mitigated through specialized construction. By applying electromagnetic flow meters specifically designed for the application, dredging engineers now achieve excellent reliability, long life and significant reduction in maintenance and operational costs.
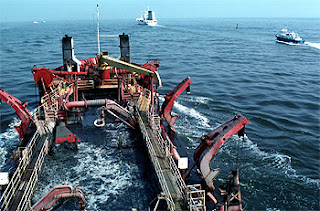
Dredging engineers always seek the simplest and most accurate method of measuring slurry flow. Considering this, there is convincing evidence that the use of customized electromagnetic flow meters, specifically designed to stand up to the rigors of dredging, look to be the best overall option.
![]() |
Dredging flow meter. (TECO) |
The dredging modifications include custom engineered ceramic brick or polyurethane liners, 3/4" stainless steel inlet and outlet protectors, independently sealed electrode wells, and field accessible Hastelloy B electrodes.
Thompson Equipment (TECO), a manufacturer of severe service magnetic flow meters located in New Orleans, will "remanufacture" any make or model of electromagnetic flow meter for dredging service. They have decades of experience servicing and remanufacturing instrumentation, and are leaders in building severe service flow meters.
Electromagnetic flow meters have always been appealing for dredging applications in terms of accuracy, resolution, and response time. Their performance problems, caused by the direct and continuous flow of abrasive slurries, are mitigated through specialized construction. By applying electromagnetic flow meters specifically designed for the application, dredging engineers now achieve excellent reliability, long life and significant reduction in maintenance and operational costs.
Selecting the Proper Flow Meter: Other Considerations
You Get What You Pay For
Engineers and maintenance personnel who purchase flow meters should remember that accurate instruments cost more based on their features and capabilities. It is always better to search for the type of flow meter best suited to a specific application before sacrificing features in favor of lower cost.
Flow meter specifiers should also take the time to examine long-term ownership costs. It may turn out that flow meters with low purchase prices may be very expensive to maintain. On the other hand, a flow meter with a high purchase price may require little or no service, and therefore lower cost of ownership over time. Lower purchase prices do not always represent the best long term, installed value.
Know Your Process
Users need to closely evaluate their overall process conditions, which include flow rates, pressure and temperature, and operating ranges. Be cautious of lower priced alternatives whose operating parameters don't fully support the requirements of the application.
All flow meters are affected to some extent by the process media and the way they are installed. As a result, their real-time performance will often be different from the controlled reference conditions under which they calibrated. There are some general rules that can be applied to flow meters to assist in reducing uncertainty:
The need for recalibration of flow meters is generally a function of how well the instrument is paired to its particular application. Should the application be critical, the flow meter accuracy should be checked at frequent, regular intervals. In some instances, mostly non-critical applications, recalibration may not be necessary for a period of years, becuase the application operating parameters never change.
Keep in mind though, that no matter what flow meter technology is chosen, overall system accuracy can never exceed the accuracy of the equipment used to perform the flow meter calibration. With that said, the most precise flow calibration systems on the market employ a positive displacement design. This type of calibrator, directly traceable to the National Institute of Standards and Technology (NIST) via water draw validation, provides total accuracy of at least 0.05 percent.
For more information on flow meter selection, installation, calibration, service, and replacement contact Thompson Equipment Company (TECO). Call them at 800-528-8997 or visit their web site at https://teco-inc.com.
Engineers and maintenance personnel who purchase flow meters should remember that accurate instruments cost more based on their features and capabilities. It is always better to search for the type of flow meter best suited to a specific application before sacrificing features in favor of lower cost.
Flow meter specifiers should also take the time to examine long-term ownership costs. It may turn out that flow meters with low purchase prices may be very expensive to maintain. On the other hand, a flow meter with a high purchase price may require little or no service, and therefore lower cost of ownership over time. Lower purchase prices do not always represent the best long term, installed value.
Know Your Process
Users need to closely evaluate their overall process conditions, which include flow rates, pressure and temperature, and operating ranges. Be cautious of lower priced alternatives whose operating parameters don't fully support the requirements of the application.
All flow meters are affected to some extent by the process media and the way they are installed. As a result, their real-time performance will often be different from the controlled reference conditions under which they calibrated. There are some general rules that can be applied to flow meters to assist in reducing uncertainty:
- For the lowest uncertainty of measurement, positive displacement meters are generally the best option.
- Electromagnetic meters provide for the widest flow range and turbine meters are usually the best choice for the highest short-term repeatability.
- Despite their high initial cost, Coriolis meters are ideal for measuring particularly viscous substances and anywhere that the measurement of mass rather than volume is required.
- In general, flow meters with few or no moving parts require less time and attention than more complex flow meters.
- Meters constructed with multiple moving parts may malfunction because of dirt, grit or grime present in the process fluid.
- Flow meters with impulse lines can also plug or corrode.
- Flow meters with flow dividers and pipe bends sometimes suffer from abrasive media wear and blockages.
- Swings in ambient temperature may affect the internal dimensions of the flow meter and could require temperature compensation.
The need for recalibration of flow meters is generally a function of how well the instrument is paired to its particular application. Should the application be critical, the flow meter accuracy should be checked at frequent, regular intervals. In some instances, mostly non-critical applications, recalibration may not be necessary for a period of years, becuase the application operating parameters never change.
Keep in mind though, that no matter what flow meter technology is chosen, overall system accuracy can never exceed the accuracy of the equipment used to perform the flow meter calibration. With that said, the most precise flow calibration systems on the market employ a positive displacement design. This type of calibrator, directly traceable to the National Institute of Standards and Technology (NIST) via water draw validation, provides total accuracy of at least 0.05 percent.
For more information on flow meter selection, installation, calibration, service, and replacement contact Thompson Equipment Company (TECO). Call them at 800-528-8997 or visit their web site at https://teco-inc.com.
TECO Valve Repair Services
TECO repairs control valves, manual valves, relief valves, actuators, and valve instrumentation. Expert, certified technicians are available to repair or recondition your valve and actuator to like-new condition.
For more information, call 800-528-8997 of visit the TECO web site at https://teco-inc.com.
Download the PDF here.
For more information, call 800-528-8997 of visit the TECO web site at https://teco-inc.com.
Download the PDF here.
Thompson Equipment is a National Stocking Distributor for ABB Rotameters (Variable Area Flowmeters)
VA Master FAM540 - The armored VA meter is ideal for the chemical, pharmaceutical and food industries.
Armored purgemeter FAM3200 - Suitable for most low flow, high pressure and corrosive applications in municipal and industrial settings.
PurgeMaster 10A6100 - Ideal for many low flow rate applications, such as purging control lines and instrument enclosures.
VA Master glass tube meters - Used for a wide variety of liquids and gases in most industrial processing facilities.
TECO (Thompson Equipment Co.) Your National Stocking Distributor
800-528-8997
NIST Traceability
Calibration means the comparison and adjustment (if necessary) of an instrument’s response to a stimulus of precisely known quantity, to ensure operational accuracy. In order to perform a calibration, one must be reasonably sure that the physical quantity used to stimulate the instrument is accurate in itself. For example, if I try calibrating a pressure gauge to read accurately at an applied pressure of 200 PSI, I must be reasonably sure that the pressure I am using to stimulate the gauge is actually 200 PSI. If it is not 200 PSI, then all I am doing is adjusting the pressure gauge to register 200 PSI when in fact it is sensing something different.
Ultimately, this is a philosophical question of epistemology: how do we know what is true? There are no easy answers here, but teams of scientists and engineers known as metrologists devote their professional lives to the study of calibration standards to ensure we have access to the best approximation of “truth” for our calibration purposes. Metrology is the science of measurement, and the central repository of expertise on this science within the United States of America is the National Institute of Standards and Technology, or the NIST (formerly known as the National Bureau of Standards, or NBS ).
Experts at the NIST work to ensure we have means of tracing measurement accuracy back to intrinsic standards, which are quantities inherently fixed (as far as anyone knows). The vibrational frequency of an isolated cesium atom when stimulated by radio energy, for example, is an intrinsic standard used for the measurement of time (forming the basis of the so-called atomic clock). So far as anyone knows, this frequency is fixed in nature and cannot vary: each and every isolated cesium atom has the exact same resonant frequency. The distance traveled in a vacuum by 1650763.73 wavelengths of light emitted by an excited krypton-86 (86Kr) atom is the intrinsic standard for one meter of length. Again, so far as anyone knows, this distance is fixed in nature and cannot vary. This means any suitably equipped laboratory in the world should be able to build their own intrinsic standards to reproduce the exact same quantities based on the same (universal) physical constants. The accuracy of an intrinsic standard is ultimately a function of nature rather than a characteristic of the device. Intrinsic standards therefore serve as absolute references which we may calibrate certain instruments against.
The machinery necessary to replicate intrinsic standards for practical use is quite expensive and usually delicate. This means the average metrologist (let alone the average industrial instrument technician) simply will never have access to one. While the concept of an intrinsic standard is tantalizing in its promise of ultimate accuracy and repeatability, it is simply beyond the reach of most laboratories to maintain.
In order for these intrinsic standards to be useful within the industrial world, we use them to calibrate other instruments, which are then used to calibrate other instruments, and so on until we arrive at the instrument we intend to calibrate for field service in a process. So long as this “chain” of instruments is calibrated against each other regularly enough to ensure good accuracy at the end-point, we may calibrate our field instruments with confidence. The documented confidence is known as NIST traceability: that the accuracy of the field instrument we calibrate is ultimately ensured by a trail of documentation leading to intrinsic standards maintained by the NIST. This “paper trail” proves to anyone interested that the accuracy of our calibrated field instruments is of the highest pedigree.
Thompson Equipment Company's calibration lab is ISO/IEC 17025 Accredited and NIST traceable.
Ultimately, this is a philosophical question of epistemology: how do we know what is true? There are no easy answers here, but teams of scientists and engineers known as metrologists devote their professional lives to the study of calibration standards to ensure we have access to the best approximation of “truth” for our calibration purposes. Metrology is the science of measurement, and the central repository of expertise on this science within the United States of America is the National Institute of Standards and Technology, or the NIST (formerly known as the National Bureau of Standards, or NBS ).
Experts at the NIST work to ensure we have means of tracing measurement accuracy back to intrinsic standards, which are quantities inherently fixed (as far as anyone knows). The vibrational frequency of an isolated cesium atom when stimulated by radio energy, for example, is an intrinsic standard used for the measurement of time (forming the basis of the so-called atomic clock). So far as anyone knows, this frequency is fixed in nature and cannot vary: each and every isolated cesium atom has the exact same resonant frequency. The distance traveled in a vacuum by 1650763.73 wavelengths of light emitted by an excited krypton-86 (86Kr) atom is the intrinsic standard for one meter of length. Again, so far as anyone knows, this distance is fixed in nature and cannot vary. This means any suitably equipped laboratory in the world should be able to build their own intrinsic standards to reproduce the exact same quantities based on the same (universal) physical constants. The accuracy of an intrinsic standard is ultimately a function of nature rather than a characteristic of the device. Intrinsic standards therefore serve as absolute references which we may calibrate certain instruments against.
The machinery necessary to replicate intrinsic standards for practical use is quite expensive and usually delicate. This means the average metrologist (let alone the average industrial instrument technician) simply will never have access to one. While the concept of an intrinsic standard is tantalizing in its promise of ultimate accuracy and repeatability, it is simply beyond the reach of most laboratories to maintain.
In order for these intrinsic standards to be useful within the industrial world, we use them to calibrate other instruments, which are then used to calibrate other instruments, and so on until we arrive at the instrument we intend to calibrate for field service in a process. So long as this “chain” of instruments is calibrated against each other regularly enough to ensure good accuracy at the end-point, we may calibrate our field instruments with confidence. The documented confidence is known as NIST traceability: that the accuracy of the field instrument we calibrate is ultimately ensured by a trail of documentation leading to intrinsic standards maintained by the NIST. This “paper trail” proves to anyone interested that the accuracy of our calibrated field instruments is of the highest pedigree.
Thompson Equipment Company's calibration lab is ISO/IEC 17025 Accredited and NIST traceable.
Reprinted from "Lessons In Industrial Instrumentation" by Tony R. Kuphaldt – under the terms and conditions of the Creative Commons Attribution 4.0 International Public License.
Subscribe to:
Posts (Atom)