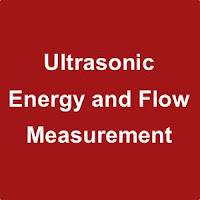 |
How Ultrasonic energy is used to measure flow. |
Ultrasonic energy
flow meters measure, via sound waves, the velocity of liquid flowing through a pipe––however, this pipe includes not just the traditional “pipe” but also mass flow chutes or something with open channels, free surfaces.
There are three different types of ultrasonic energy measuring tools, called flow meters: the first is the Open Channel flow meter which receives its calculations by computing geometrical distance; the second is the Doppler shift flow meter which reflects ultrasonic beams off sonically reflective materials, e.g. air bubbles; the third is the contrapropogating transit-time flow meter or, more recognizably, the transmission flow meter. The transmission flow meter has two versions: the in-line and the clamp-on. The former is “intrusive” whereas the latter is not, an outward device. These 72+ inch tools, using ultrasound technology, have the ability to measure fluids in bulk, all with distinct properties and principles., The use of this technology is most used in the respective oil and nuclear industries, wastewater technologies, pharmaceutical applications, and the food and beverage industry.
For intrusive flow meters, sensors are fitted opposite one another and alternate bouncing ultrasonic signals back and forth in the pipe, in an almost tennis-like format. In an elementary explanation, by increasing the number of sensors, engineers are able to decipher flow proportions through calculations of velocity between sensory transmissions; thereby, the flow volume can be computed.
For unintrusive flow meters, a literal clamp-on flow meter is placed atop the pipe so as not to interrupt flow. One of the most special properties uninstrusive flow meters offer is the ability to bounce ultrasonic sensors through piping up to four meters in diameter; this makes seemingly impossible feats possible, especially in otherwise difficult fields, e.g. hydroelectric.
Although the technology is pervasive, there are disadvantages still as there are advantages. However, the majority of the equipment’s disadvantages are unavoidable, such as costs and apparatus sensitivities. Nonetheless, there is also the threat of low ultrasonic accuracy, or attenuation, dependent on what systems are used and under what circumstances and command. Alternatively, one of the most publicized advantages is that ultrasonic energy flow technology is used for custody transfer of natural gases and petroleum liquids. Custody transfer usually entails following industry, national, and government standards and regulations. Ultrasonic energy flowmeters and analyzers are also relatively low maintenance, e.g. self-diagnosing. The technology has the capability to control and manage high pressures as well as high temperatures, and, being a popular application among engineers, manufacturers and the like, is reliable in its performance and consistency.
For more information on any industrial flow application, contact
TECO at 800-528-8997 or visit
www.teco-inc.com.